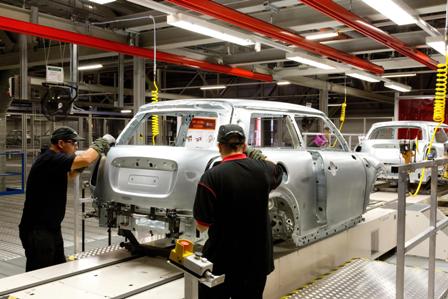
An all-new vehicle platform, a range of new technologies and a £750 million investment across three of BMW Group’s UK manufacturing facilities herald the launch of the new 2014 MINI. Substantial upgrades to Plant Oxford, where MINIs are assembled, and to Plant Swindon, where most of the MINI’s body pressings and sub-assemblies are manufactured, mark the start of an exciting new phase in the MINI’s development. The Hams Hall engine plant in Birmingham is also being re-equipped.
This latest MINI also debuts a vital and highly flexible new platform family within the BMW Group. A new approach to platform design increases the flexibility of the body manufacturing process, allowing more derivatives of greater conceptual variation to be produced more efficiently, an essential element of the MINI’s build-to-order appeal.
Further investment highlights include a new 1000-robot bodyshop at Plant Oxford and the debut of various new body-in-white technologies at Plant Swindon. The Hams Hall engine plant is also being freshly equipped for a new generation of modular power units that will be manufactured at several locations, the Birmingham plant supplying crankshafts to all these factories. These new engines, the new platform and a completely refreshed design have produced a completely new MINI.
Harald Krüger, member of the BMW Group Board of Management, said, “In our Oxford plant’s centenary year, we are continuing the MINI brand success story and today starting production of the new model generation. Our total investment of £750 million in our British production locations of Oxford, Swindon and Hams Hall between 2012 and 2015 underscores the importance of the MINI production triangle within our global production network. The UK is the heart of MINI production – thanks to the experience, competence and strong commitment of all our employees.”
Peter Schwarzenbauer, Member of the BMW Group Board of Management, said, “The MINI brand represents the marriage of innovation and tradition. It is the inspiration for trendsetters and creative types all over the world. The aim of the new MINI generation is once again to rekindle enthusiasm for this car. That is why we are offering even more individual features, for example, to ensure that every new MINI is a statement of the owner’s personality.”
Plant Oxford, which celebrates 100 years of car-making in 2013, remains at the heart of the MINI manufacturing network, and receives the lion’s share of the £750 million investment. Besides a new state-of-the-art bodyshop, the plant also benefits from upgrades to its quality validation processes, to its paintshop and from a series of initiatives reducing the operation’s carbon footprint and improving its waste management processes.
Plant Swindon has also benefitted from investment that sees it debuting a trio of new body manufacturing technologies. It has also received facility improvements that will increase its productivity and help maintain its excellent showing among independent reviews of automotive manufacturing efficiency.
Plant Oxford
New Bodyshop
An army of no less than 1000 new robots will assemble the bodies of the new MINI in a brand new, purpose-built bodyshop at Plant Oxford. The factory’s body-in-white facilities now extend to 100,000m2. This impressive new body assembly facility accounts for a significant portion of the £750 million that BMW has invested in the third-generation new MINI, its robots not only ensuring that bodies are consistently assembled to an exceptional level of precision, but can also cater for the wide choice of models for which MINI has become famous.
To this end the robots are arranged around three-framing stages rather than the usual two, this body assembly method allowing a greater variety of body styles than was previously feasible. This flexible platform concept also utilises a higher number of smaller panels, than previously – 435, in the case of the new MINI hatchback – these requiring more spot-welds as a consequence.
A typical MINI body shell now receives between 4000 and 6000 spot-welds, to produce a rigid and immensely strong base architecture that enables a wider variety of surrounding body panels to be attached with a particularly high degree of accuracy.
This new platform concept is also more weight efficient. At certain stations no less than eight robots work on a single body simultaneously, operating on three different levels. The assembly accuracy of every single body is measured using Perceptron cameras that measure to an accuracy of 0.05mm, or half the width of a human hair. They measure the body across 502 datum points at five stations during the body-in-white assembly process.
The new bodyshop is also unusual for operating a single common finished process system. Whereas most bodyshops operate two identical lines in parallel, Plant Oxford’s bodyshop functions as a single line, everybody undergoing the same process at the hands of the same operators and machines. The advantage is more consistent quality and greater efficiency.
Besides the 1000 robots, BMW has also invested in 1000 grippers, these being the mechanisms that enable the robots to handle the tools and wide variety of body panels needed to assemble a very wide range of MINI derivatives. These ingeniously-designed bespoke handling mechanisms are often more expensive than the robots that deploy them. The robots operate using the latest programmed logic controllers and some of them have the ability to ‘see’, their intelligence allowing them to pick components from a part-empty box, for example. Less intelligent robots need to detect a full box of components before they can start their cycle.
Paint Shop
Plant Oxford was the first BMW Group plant to use the environmentally friendly Integrated Paint Process (IPP), which completely eliminates the primer coat application and oven stage to yield energy savings and a reduction in paintshop emissions of well over 10%. The shop now benefits from two additional quality-enhancing new developments. One involves further automation of the seam-sealing process, while the other sees the further robotisation of the application of a MINI’s top-coat. Both developments improve quality and reduce waste.
The new seam-sealing system sees welded joints in the car’s interior, engine bay, its roof and part of the tailgate aperture automatically protected against water-ingress with a flexible mastic material applied by a set of 12 robots. Besides reducing the risk of corrosion, this process also limits the passage of noise into the car.
Automation ensures that the application of the mastic is performed to a consistently high quality and with less material waste. Automation has also been introduced to the application of top-coat to the door, tailgate and bonnet apertures, ensuring a consistently high standard of finish, and less paint wastage. Productivity also improves with the introduction of the nine robots that perform these tasks. The energy efficiency of the paint shop has also been improved by the introduction of a new oven temperature control system requiring less gas.
The new MINI now features a double-skinned front bulkhead separating the engine bay from the passenger compartment. The double skin reduces the passage of noise into the cabin, its effectiveness significantly enhanced by the robot injection of foam into this void. Robots inject two chemicals that when mixed, combine to form a foam that rapidly expands into the available space to create dense, lightweight and highly effective sound-deadening structure that also strengthens the body.
Quality Management
There are over 3,600 components in a new MINI. There is considerable science behind ensuring that they fit together precisely right first time, and stay that way through the lifetime of the car. The science is performed by MINI Plant Oxford’s quality and engineering department, and also drawn upon by Plant Swindon.
The department uses some highly sophisticated measuring equipment that now includes a Geometric Optical Measurement Cell. The cameras of this cell can record an extraordinary eight million megapixel images, each of these pixels representing a datum point allowing a car – or a component – to be measured with exceptional accuracy. A series of these images can be knitted together with very high precision to produce a 3-D picture of the entire car and every area within it. Colour-imaging reveals the dimensional compliance of a MINI’s every element, from an entire panel to a single bolt. It provides an extremely accurate way of measuring a large volume and, among other things, is used for aligning the holes for fixings, ensuring the correct gaps between components and that parts follow the correct sculptural profile. The ultimate objective is to ensure that the car and its constituent parts comply with the original computer-aided design drawings, a process that’s fundamental to the accurate manufacture of a new car.
At the very heart of the quality and engineering centre lies the so-called Cube, an aluminium master buck that is a full-size replica of the new MINI. Built to a tolerance of just one fifth of a millimetre, this is the template for the body and everything attached to it, the buck itself attached to a thick, steel-plate floor that is absolutely horizontal for accuracy. Besides ensuring that the new MINI is born to millimetre-accuracy, the Cube is used to ensure that the car remains precisely manufactured throughout its life.
Assembly
A substantial investment programme has produced significant improvements in the Plant Oxford assembly hall. There are now height-adjustable skillets on two production lines to ease the assembly process, while 44 automated guided vehicles (AGVs) carry pre-assembled cockpits to the track. There are six new robots in the glazing cell, two of them equipped with cameras allowing them to see and identify different derivatives, while the sunroof installation facility is now fully automated. Cameras are also used to ensure the accuracy of the process marrying the engine to the car.
Swindon
The Swindon body pressings and sub-assembly plant benefits from upgrades that debut several new technologies, besides producing efficiency improvements.
Tactile laser welding is one of the new technologies, this technique used to weld together the eight different pressed parts that make up the complex bonnet panel that is such a distinctive feature of the MINI. This innovative technique involves the bending of the edge bonnet’s outer panel to the point where it touches the mating flange on the inner panel. The two are then joined using a fine weld wire on the laser that creates a continuous and solid joint. Under the previous system the panels were roller-hemmed together, and although this process was supplemented with adhesive and seam sealer to provide corrosion protection, there was always the possibility of a void forming that could allow rust-promoting condensation to develop. That risk is now eliminated.
Another innovation is the development of a remote laser that can produce long continuous joints of greater precision, a process that is also quicker than spot-welding and a first for the BMW Group.
Also new is a facility that enables up to five different door designs to be produced in the same production cell by the same set of robots using a new fixture-holding system. Assembling such a wide range of designs on the same hardware is complex, but it’s more efficient. A new linear change system for switching the tooling from one model to another has also increased efficiency.
Plant Swindon’s key press lines have been upgraded using a smart investment model that has produced a significant update following substantial investment. Some of these presses have been in the plant for many years with a life almost as long as the plant itself, but clever refurbishment is extending their term of service with no penalty in terms of quality, reliability or efficiency. This smart investment approach has contributed to Swindon’s excellent rating in influential analyses assessing global automotive production efficiency.
The plant has also met the challenge of designing tooling to suit the unique styling of the MINI, some of this iconic car’s detailing requiring clever tool engineering to allow its design to be realised. An example is the new tailgate, which has cut-outs in its sides to accommodate the new tail lamp style. Few owners will realise the how challenging this has been to achieve, but the result is impressively tight and consistent panel-fit.
Sustainability
BMW Group is currently operating no less than 730 programmes designed to reduce the carbon footprint and waste generated by all its manufacturing operations in the UK, some 279 of these deployed across the MINI Plant Oxford and Plant Swindon operations.
Particularly innovative is an ingenious new electro-coating facility. Electro-coat is the first protective layer of paint applied to the car’s panels using an electrically-charged dip to ensure that protective paint reaches every crevice within the body. The previous system featured a three-stage bath, this replaced by a 12-stage bath system that is able to apply precisely the right thickness of paint to each area of the body. Some zones are more vulnerable to corrosion than others, this new system also catering for the different shapes of each MINI body variant. The aim is to apply precisely the right amount of paint for each body style, yielding savings in both materials and energy whilst maintaining excellent corrosion protection.
Plant Oxford’s new bodyshop also makes a significant contribution to the factory’s environmental performance. The new building itself is very well insulated to reduce the cost of air conditioning, while the robots it houses now have an energy-saving sleep mode. So-called heat wheels in the building’s roof control the recirculation and admission of fresh air to reduce the amount of heating and cooling required. The bodyshop also employs water-harvesting to supply all the toilets, and each of its 3869 lights is individually programmable.
Controlling the flow of air through the paint shop with greater precision has yielded a 730 tonne saving in CO2 production thanks to reduced gas usage, and a 1130 tonne CO2 saving from reduced electricity consumption. And a programme to more carefully control the level of humidity in the paintshop – a certain level of humidity is essential to the painting process – has yielded a saving of 420 tonnes of CO2 annually. During 2013, the combined impact of 175 energy-saving initiatives at Plant Oxford and Plant Swindon will yield savings of almost 47.8GWh of energy savings of almost, which is roughly equivalent to the energy consumed by 2390 average UK homes in a year.
The 44 AGVs used in the assembly hall are powered by electric capacitors, which have three times the life of a conventional battery and are more energy efficient.
People
New investment and facilities are vital to a plant’s industrial competitiveness, but their potential cannot be realised without the ingenuity, commitment and flexibility of the people working there. Who have willingly adapted their working days to allow for the extensive remodelling of Plant Oxford, while at Plant Swindon the staff have pioneered new body engineering techniques to satisfy the design requirements for the new MINI. And both plants developed flexible new working methods that allow supply to better meet demand.
Education and training are also an essential part of BMW’s commitment to its workforce. Significant sums have recently been invested in ‘Performing Manufacturing Operations’ training. PMO training focuses on ensuring that associates work in a safe environment, can adhere to processes and standards and ultimately results in a National Vocational Qualification (NVQ) level 2 qualification. This undertaking has produced the most extensive training programme Plant Oxford and Swindon have yet seen, to assist all production associates in their preparation to build the next new MINI.
Plant Oxford has also developed a new bespoke training facility, primarily for apprentice training. Opened in 2012, it enables the company to tailor the education of our apprentices, both academic and practical, to better match the needs of the business in the future. Apprentice training leads to an NVQ level three qualification and some apprentices will have the opportunity to progress right through to degree level.
New MINI production at Oxford and Swindon
19 Nov 2013
An all-new vehicle platform, a range of new technologies and a £750 million investment across three of BMW Group’s UK manufacturing facilities herald the launch of the new 2014 MINI. Substantial upgrades to Plant Oxford, where MINIs are assembled, and to Plant Swindon, where most of the MINI’s body pressings and sub-assemblies are manufactured, mark the start of an exciting new phase in the MINI’s development. The Hams Hall engine plant in Birmingham is also being re-equipped.
This latest MINI also debuts a vital and highly flexible new platform family within the BMW Group. A new approach to platform design increases the flexibility of the body manufacturing process, allowing more derivatives of greater conceptual variation to be produced more efficiently, an essential element of the MINI’s build-to-order appeal.
Further investment highlights include a new 1000-robot bodyshop at Plant Oxford and the debut of various new body-in-white technologies at Plant Swindon. The Hams Hall engine plant is also being freshly equipped for a new generation of modular power units that will be manufactured at several locations, the Birmingham plant supplying crankshafts to all these factories. These new engines, the new platform and a completely refreshed design have produced a completely new MINI.
Harald Krüger, member of the BMW Group Board of Management, said, “In our Oxford plant’s centenary year, we are continuing the MINI brand success story and today starting production of the new model generation. Our total investment of £750 million in our British production locations of Oxford, Swindon and Hams Hall between 2012 and 2015 underscores the importance of the MINI production triangle within our global production network. The UK is the heart of MINI production – thanks to the experience, competence and strong commitment of all our employees.”
Peter Schwarzenbauer, Member of the BMW Group Board of Management, said, “The MINI brand represents the marriage of innovation and tradition. It is the inspiration for trendsetters and creative types all over the world. The aim of the new MINI generation is once again to rekindle enthusiasm for this car. That is why we are offering even more individual features, for example, to ensure that every new MINI is a statement of the owner’s personality.”
Plant Oxford, which celebrates 100 years of car-making in 2013, remains at the heart of the MINI manufacturing network, and receives the lion’s share of the £750 million investment. Besides a new state-of-the-art bodyshop, the plant also benefits from upgrades to its quality validation processes, to its paintshop and from a series of initiatives reducing the operation’s carbon footprint and improving its waste management processes.
Plant Swindon has also benefitted from investment that sees it debuting a trio of new body manufacturing technologies. It has also received facility improvements that will increase its productivity and help maintain its excellent showing among independent reviews of automotive manufacturing efficiency.
Plant Oxford
New Bodyshop
An army of no less than 1000 new robots will assemble the bodies of the new MINI in a brand new, purpose-built bodyshop at Plant Oxford. The factory’s body-in-white facilities now extend to 100,000m2. This impressive new body assembly facility accounts for a significant portion of the £750 million that BMW has invested in the third-generation new MINI, its robots not only ensuring that bodies are consistently assembled to an exceptional level of precision, but can also cater for the wide choice of models for which MINI has become famous.
To this end the robots are arranged around three-framing stages rather than the usual two, this body assembly method allowing a greater variety of body styles than was previously feasible. This flexible platform concept also utilises a higher number of smaller panels, than previously – 435, in the case of the new MINI hatchback – these requiring more spot-welds as a consequence.
A typical MINI body shell now receives between 4000 and 6000 spot-welds, to produce a rigid and immensely strong base architecture that enables a wider variety of surrounding body panels to be attached with a particularly high degree of accuracy.
This new platform concept is also more weight efficient. At certain stations no less than eight robots work on a single body simultaneously, operating on three different levels. The assembly accuracy of every single body is measured using Perceptron cameras that measure to an accuracy of 0.05mm, or half the width of a human hair. They measure the body across 502 datum points at five stations during the body-in-white assembly process.
The new bodyshop is also unusual for operating a single common finished process system. Whereas most bodyshops operate two identical lines in parallel, Plant Oxford’s bodyshop functions as a single line, everybody undergoing the same process at the hands of the same operators and machines. The advantage is more consistent quality and greater efficiency.
Besides the 1000 robots, BMW has also invested in 1000 grippers, these being the mechanisms that enable the robots to handle the tools and wide variety of body panels needed to assemble a very wide range of MINI derivatives. These ingeniously-designed bespoke handling mechanisms are often more expensive than the robots that deploy them. The robots operate using the latest programmed logic controllers and some of them have the ability to ‘see’, their intelligence allowing them to pick components from a part-empty box, for example. Less intelligent robots need to detect a full box of components before they can start their cycle.
Paint Shop
Plant Oxford was the first BMW Group plant to use the environmentally friendly Integrated Paint Process (IPP), which completely eliminates the primer coat application and oven stage to yield energy savings and a reduction in paintshop emissions of well over 10%. The shop now benefits from two additional quality-enhancing new developments. One involves further automation of the seam-sealing process, while the other sees the further robotisation of the application of a MINI’s top-coat. Both developments improve quality and reduce waste.
The new seam-sealing system sees welded joints in the car’s interior, engine bay, its roof and part of the tailgate aperture automatically protected against water-ingress with a flexible mastic material applied by a set of 12 robots. Besides reducing the risk of corrosion, this process also limits the passage of noise into the car.
Automation ensures that the application of the mastic is performed to a consistently high quality and with less material waste. Automation has also been introduced to the application of top-coat to the door, tailgate and bonnet apertures, ensuring a consistently high standard of finish, and less paint wastage. Productivity also improves with the introduction of the nine robots that perform these tasks. The energy efficiency of the paint shop has also been improved by the introduction of a new oven temperature control system requiring less gas.
The new MINI now features a double-skinned front bulkhead separating the engine bay from the passenger compartment. The double skin reduces the passage of noise into the cabin, its effectiveness significantly enhanced by the robot injection of foam into this void. Robots inject two chemicals that when mixed, combine to form a foam that rapidly expands into the available space to create dense, lightweight and highly effective sound-deadening structure that also strengthens the body.
Quality Management
There are over 3,600 components in a new MINI. There is considerable science behind ensuring that they fit together precisely right first time, and stay that way through the lifetime of the car. The science is performed by MINI Plant Oxford’s quality and engineering department, and also drawn upon by Plant Swindon.
The department uses some highly sophisticated measuring equipment that now includes a Geometric Optical Measurement Cell. The cameras of this cell can record an extraordinary eight million megapixel images, each of these pixels representing a datum point allowing a car – or a component – to be measured with exceptional accuracy. A series of these images can be knitted together with very high precision to produce a 3-D picture of the entire car and every area within it. Colour-imaging reveals the dimensional compliance of a MINI’s every element, from an entire panel to a single bolt. It provides an extremely accurate way of measuring a large volume and, among other things, is used for aligning the holes for fixings, ensuring the correct gaps between components and that parts follow the correct sculptural profile. The ultimate objective is to ensure that the car and its constituent parts comply with the original computer-aided design drawings, a process that’s fundamental to the accurate manufacture of a new car.
At the very heart of the quality and engineering centre lies the so-called Cube, an aluminium master buck that is a full-size replica of the new MINI. Built to a tolerance of just one fifth of a millimetre, this is the template for the body and everything attached to it, the buck itself attached to a thick, steel-plate floor that is absolutely horizontal for accuracy. Besides ensuring that the new MINI is born to millimetre-accuracy, the Cube is used to ensure that the car remains precisely manufactured throughout its life.
Assembly
A substantial investment programme has produced significant improvements in the Plant Oxford assembly hall. There are now height-adjustable skillets on two production lines to ease the assembly process, while 44 automated guided vehicles (AGVs) carry pre-assembled cockpits to the track. There are six new robots in the glazing cell, two of them equipped with cameras allowing them to see and identify different derivatives, while the sunroof installation facility is now fully automated. Cameras are also used to ensure the accuracy of the process marrying the engine to the car.
Swindon
The Swindon body pressings and sub-assembly plant benefits from upgrades that debut several new technologies, besides producing efficiency improvements.
Tactile laser welding is one of the new technologies, this technique used to weld together the eight different pressed parts that make up the complex bonnet panel that is such a distinctive feature of the MINI. This innovative technique involves the bending of the edge bonnet’s outer panel to the point where it touches the mating flange on the inner panel. The two are then joined using a fine weld wire on the laser that creates a continuous and solid joint. Under the previous system the panels were roller-hemmed together, and although this process was supplemented with adhesive and seam sealer to provide corrosion protection, there was always the possibility of a void forming that could allow rust-promoting condensation to develop. That risk is now eliminated.
Another innovation is the development of a remote laser that can produce long continuous joints of greater precision, a process that is also quicker than spot-welding and a first for the BMW Group.
Also new is a facility that enables up to five different door designs to be produced in the same production cell by the same set of robots using a new fixture-holding system. Assembling such a wide range of designs on the same hardware is complex, but it’s more efficient. A new linear change system for switching the tooling from one model to another has also increased efficiency.
Plant Swindon’s key press lines have been upgraded using a smart investment model that has produced a significant update following substantial investment. Some of these presses have been in the plant for many years with a life almost as long as the plant itself, but clever refurbishment is extending their term of service with no penalty in terms of quality, reliability or efficiency. This smart investment approach has contributed to Swindon’s excellent rating in influential analyses assessing global automotive production efficiency.
The plant has also met the challenge of designing tooling to suit the unique styling of the MINI, some of this iconic car’s detailing requiring clever tool engineering to allow its design to be realised. An example is the new tailgate, which has cut-outs in its sides to accommodate the new tail lamp style. Few owners will realise the how challenging this has been to achieve, but the result is impressively tight and consistent panel-fit.
Sustainability
BMW Group is currently operating no less than 730 programmes designed to reduce the carbon footprint and waste generated by all its manufacturing operations in the UK, some 279 of these deployed across the MINI Plant Oxford and Plant Swindon operations.
Particularly innovative is an ingenious new electro-coating facility. Electro-coat is the first protective layer of paint applied to the car’s panels using an electrically-charged dip to ensure that protective paint reaches every crevice within the body. The previous system featured a three-stage bath, this replaced by a 12-stage bath system that is able to apply precisely the right thickness of paint to each area of the body. Some zones are more vulnerable to corrosion than others, this new system also catering for the different shapes of each MINI body variant. The aim is to apply precisely the right amount of paint for each body style, yielding savings in both materials and energy whilst maintaining excellent corrosion protection.
Plant Oxford’s new bodyshop also makes a significant contribution to the factory’s environmental performance. The new building itself is very well insulated to reduce the cost of air conditioning, while the robots it houses now have an energy-saving sleep mode. So-called heat wheels in the building’s roof control the recirculation and admission of fresh air to reduce the amount of heating and cooling required. The bodyshop also employs water-harvesting to supply all the toilets, and each of its 3869 lights is individually programmable.
Controlling the flow of air through the paint shop with greater precision has yielded a 730 tonne saving in CO2 production thanks to reduced gas usage, and a 1130 tonne CO2 saving from reduced electricity consumption. And a programme to more carefully control the level of humidity in the paintshop – a certain level of humidity is essential to the painting process – has yielded a saving of 420 tonnes of CO2 annually. During 2013, the combined impact of 175 energy-saving initiatives at Plant Oxford and Plant Swindon will yield savings of almost 47.8GWh of energy savings of almost, which is roughly equivalent to the energy consumed by 2390 average UK homes in a year.
The 44 AGVs used in the assembly hall are powered by electric capacitors, which have three times the life of a conventional battery and are more energy efficient.
People
New investment and facilities are vital to a plant’s industrial competitiveness, but their potential cannot be realised without the ingenuity, commitment and flexibility of the people working there. Who have willingly adapted their working days to allow for the extensive remodelling of Plant Oxford, while at Plant Swindon the staff have pioneered new body engineering techniques to satisfy the design requirements for the new MINI. And both plants developed flexible new working methods that allow supply to better meet demand.
Education and training are also an essential part of BMW’s commitment to its workforce. Significant sums have recently been invested in ‘Performing Manufacturing Operations’ training. PMO training focuses on ensuring that associates work in a safe environment, can adhere to processes and standards and ultimately results in a National Vocational Qualification (NVQ) level 2 qualification. This undertaking has produced the most extensive training programme Plant Oxford and Swindon have yet seen, to assist all production associates in their preparation to build the next new MINI.
Plant Oxford has also developed a new bespoke training facility, primarily for apprentice training. Opened in 2012, it enables the company to tailor the education of our apprentices, both academic and practical, to better match the needs of the business in the future. Apprentice training leads to an NVQ level three qualification and some apprentices will have the opportunity to progress right through to degree level.