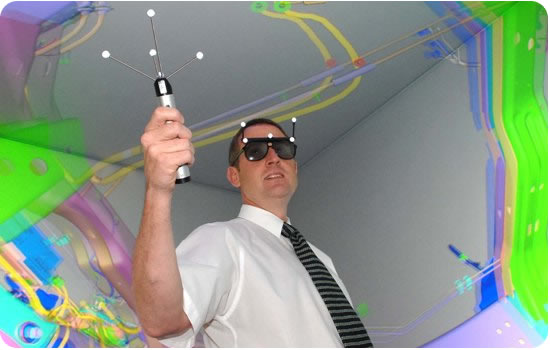
Jaguar Land Rover’s ultra-modern virtual reality engineering and design studio has saved the group more than three times its cost in two years of operation by cutting the time and costs normally associated with vehicle development.
Commissioned in late 2007 and first used in 2008, the virtual reality system has saved more than £8m in vehicle development costs.
Working in virtual reality has begun a revolution in how Jaguar Land Rover designs its cars. The computer simulations allow engineers to visualize full-size 3D models of components – and even the entire vehicle – long before physical parts are available.
The latest Jaguars and Land Rovers, like the new Jaguar XJ saloon and the Range Rover Evoque, have already benefited from the virtual reality studio. The high-resolution 3D images enable engineers and designers to work on features both inside and outside the car, and the system can make bodywork appear transparent to reveal the parts and systems underneath.
The virtual reality studio has proved invaluable for a wide range of tasks. These include reviewing the exterior and interior designs; optimising interior space, visibility and control layout; developing aerodynamics and crash performance; analysing the routing of wiring and pipework; and analysing manufacturing and assembly processes.
Using the virtual reality system for all these functions vastly reduces the number of costly physical prototypes and models that need to be built during the development of a car, as well as cutting the number of miles covered in prototypes.
A reduction in the number of physical prototypes built also means vehicle development is much more time-efficient too. This is a vital point as cars become more technologically complex, yet competitive business pressures to get new models to market increase.
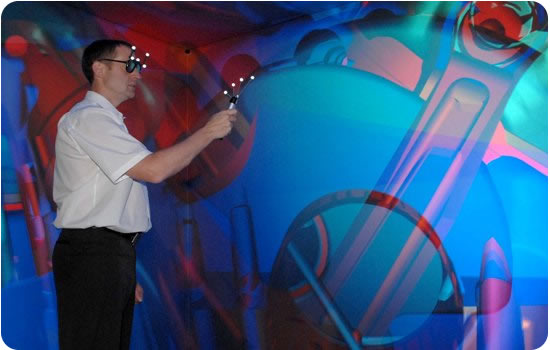
As Ian Anderton, advanced engineering programme manager, explains: “While the time taken to develop a car is still about three years, the greater complexity of vehicles has significantly increased the amount of work required. The virtual reality system helps us to ensure that we still deliver the highest quality products, because we’re using our time in a much more efficient way.”
One area where the virtual reality system can prove very useful is in clash detection – making sure that components fit into a car without interfering with each other.
“The system allows you to instantly see if something will work – such as putting in a different exhaust unit or fitting brake lines. But it’s also useful for checking if items will fit in the car, such as a set of golf clubs or even cups in cup holders,” adds Anderton.
Clash detection is also useful in areas beyond vehicle construction. It’s also used to make sure a car can be serviced when it’s in the garage with the maximum ease.
Refining the interior design provides another example of the value of 3D modelling. The system allows designers to ‘sit’ in a vehicle and see how a planned layout of, for instance, a dashboard could be used by the driver, again saving huge amounts of time and money creating physical models.
Jaguar Land Rover’s virtual reality studio is thought to be the world’s most advanced virtual reality facility within the automotive industry.
The studio is known as the ‘cave’ because it looks like an empty room, with three of the sides and the ceiling acting as ‘screens’ for 3D projection of the computer generated models.
The cave uses two Sony digital cinema projectors per screen to display 3D images that are four times the resolution of HD TV. These eight projectors are powered by 16 high performance PCs. Indeed, each of these PCs is approximately three times as powerful as a modern high-spec desktop machine.
In addition to these 16 PCs, there are also two additional machines. The first processes the CAD data that goes to the projector PCs and the second machine records output data.
The virtual reality cave allows an operator wearing 3D glasses to manipulate images using a wand, not too dissimilar to a modern games console controller.
These simple, visual controls make the system easy to learn and operate. The basics can be picked up within 20 minutes – enough to run a meeting in the virtual cave – while two hours is enough to learn the more complex operating system including loading new diagrams to the system.
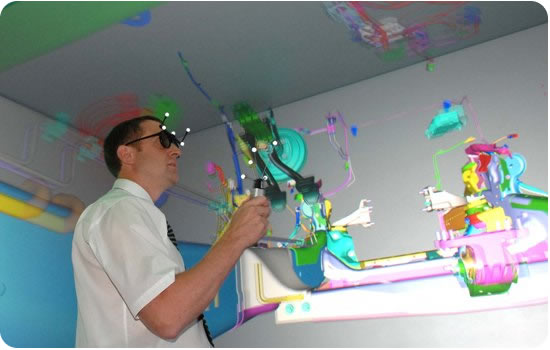
“While 3D digital models of new vehicles have existed for a while, they were difficult to visualise and manipulate. Using the cave makes it much easier and faster to look at the complete vehicle, carry out updates and see how things are developing,” says Anderton.
“As changes are made, they can be uploaded from anywhere in the building and viewed instantly.”
The power and flexibility of the system is such that it is not just restricted to vehicles. Providing the CAD data is available, then anything can be displayed in the virtual reality cave, including buildings.
JLR has used the cave to help with the design of new dealerships to make sure vehicles will fit inside and can be manoeuvred with plenty of clearance.
“We’ve also got part of the Solihull production line on the system. We used this to check two things: firstly, that line workers can assemble the cars safely and efficiently, and secondly, to check that new machinery has sufficient space within the building layout,” says VR Centre Manager Brian Waterfield.
Another unexpected bonus is that Jaguar Land Rover has found the virtual reality cave provides an inspiration to students and young engineers.
“We’ve had visits from schools and had very positive feedback with a lot of kids saying they then want to go into engineering,” says Waterfield. “A lot of this is because kids are used to games consoles and can see that some of the technology we’re using is similar to that in Xboxes, Wiis or Playstations.”
While Jaguar Land Rover’s virtual reality cave may not be a full-on car simulator like a video game, it certainly represents a major step forward in the way vehicles are developed.
Jaguar Land Rover’s Virtual Cave
8 Nov 2010
Jaguar Land Rover’s ultra-modern virtual reality engineering and design studio has saved the group more than three times its cost in two years of operation by cutting the time and costs normally associated with vehicle development.
Commissioned in late 2007 and first used in 2008, the virtual reality system has saved more than £8m in vehicle development costs.
Working in virtual reality has begun a revolution in how Jaguar Land Rover designs its cars. The computer simulations allow engineers to visualize full-size 3D models of components – and even the entire vehicle – long before physical parts are available.
The latest Jaguars and Land Rovers, like the new Jaguar XJ saloon and the Range Rover Evoque, have already benefited from the virtual reality studio. The high-resolution 3D images enable engineers and designers to work on features both inside and outside the car, and the system can make bodywork appear transparent to reveal the parts and systems underneath.
The virtual reality studio has proved invaluable for a wide range of tasks. These include reviewing the exterior and interior designs; optimising interior space, visibility and control layout; developing aerodynamics and crash performance; analysing the routing of wiring and pipework; and analysing manufacturing and assembly processes.
Using the virtual reality system for all these functions vastly reduces the number of costly physical prototypes and models that need to be built during the development of a car, as well as cutting the number of miles covered in prototypes.
A reduction in the number of physical prototypes built also means vehicle development is much more time-efficient too. This is a vital point as cars become more technologically complex, yet competitive business pressures to get new models to market increase.
As Ian Anderton, advanced engineering programme manager, explains: “While the time taken to develop a car is still about three years, the greater complexity of vehicles has significantly increased the amount of work required. The virtual reality system helps us to ensure that we still deliver the highest quality products, because we’re using our time in a much more efficient way.”
One area where the virtual reality system can prove very useful is in clash detection – making sure that components fit into a car without interfering with each other.
“The system allows you to instantly see if something will work – such as putting in a different exhaust unit or fitting brake lines. But it’s also useful for checking if items will fit in the car, such as a set of golf clubs or even cups in cup holders,” adds Anderton.
Clash detection is also useful in areas beyond vehicle construction. It’s also used to make sure a car can be serviced when it’s in the garage with the maximum ease.
Refining the interior design provides another example of the value of 3D modelling. The system allows designers to ‘sit’ in a vehicle and see how a planned layout of, for instance, a dashboard could be used by the driver, again saving huge amounts of time and money creating physical models.
Jaguar Land Rover’s virtual reality studio is thought to be the world’s most advanced virtual reality facility within the automotive industry.
The studio is known as the ‘cave’ because it looks like an empty room, with three of the sides and the ceiling acting as ‘screens’ for 3D projection of the computer generated models.
The cave uses two Sony digital cinema projectors per screen to display 3D images that are four times the resolution of HD TV. These eight projectors are powered by 16 high performance PCs. Indeed, each of these PCs is approximately three times as powerful as a modern high-spec desktop machine.
In addition to these 16 PCs, there are also two additional machines. The first processes the CAD data that goes to the projector PCs and the second machine records output data.
The virtual reality cave allows an operator wearing 3D glasses to manipulate images using a wand, not too dissimilar to a modern games console controller.
These simple, visual controls make the system easy to learn and operate. The basics can be picked up within 20 minutes – enough to run a meeting in the virtual cave – while two hours is enough to learn the more complex operating system including loading new diagrams to the system.
“While 3D digital models of new vehicles have existed for a while, they were difficult to visualise and manipulate. Using the cave makes it much easier and faster to look at the complete vehicle, carry out updates and see how things are developing,” says Anderton.
“As changes are made, they can be uploaded from anywhere in the building and viewed instantly.”
The power and flexibility of the system is such that it is not just restricted to vehicles. Providing the CAD data is available, then anything can be displayed in the virtual reality cave, including buildings.
JLR has used the cave to help with the design of new dealerships to make sure vehicles will fit inside and can be manoeuvred with plenty of clearance.
“We’ve also got part of the Solihull production line on the system. We used this to check two things: firstly, that line workers can assemble the cars safely and efficiently, and secondly, to check that new machinery has sufficient space within the building layout,” says VR Centre Manager Brian Waterfield.
Another unexpected bonus is that Jaguar Land Rover has found the virtual reality cave provides an inspiration to students and young engineers.
“We’ve had visits from schools and had very positive feedback with a lot of kids saying they then want to go into engineering,” says Waterfield. “A lot of this is because kids are used to games consoles and can see that some of the technology we’re using is similar to that in Xboxes, Wiis or Playstations.”
While Jaguar Land Rover’s virtual reality cave may not be a full-on car simulator like a video game, it certainly represents a major step forward in the way vehicles are developed.